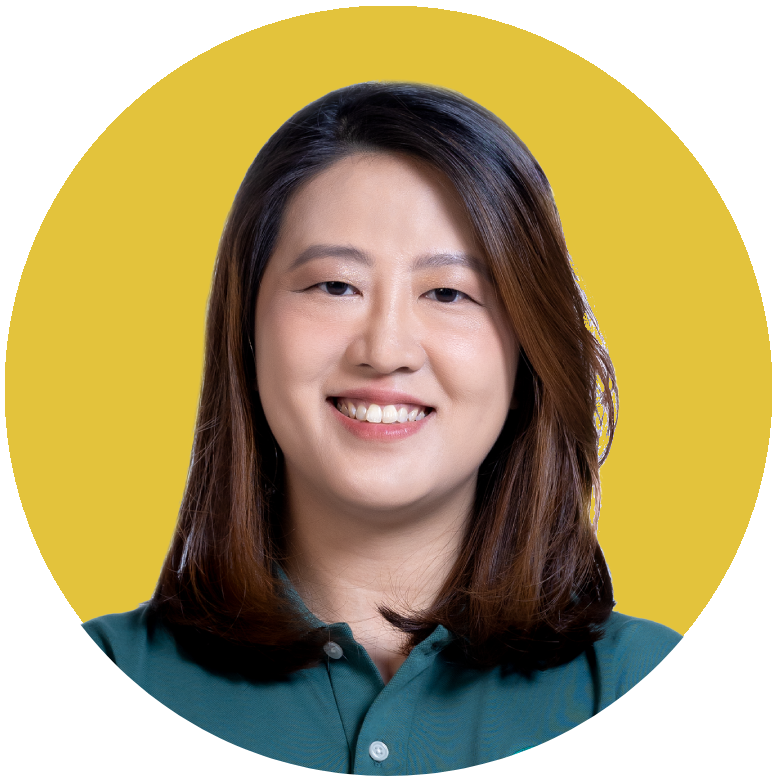
Lead ergonomist
In 2021, the company called in Ergo Global to help with a growing number of musculoskeletal disorders (MSDs) and staff reporting bodily discomfort in the last 12 months within their Singapore laboratory. Abbott were looking for both short and long term solutions to this, along with assistance in becoming totally compliant with local laws throughout the facility.
Upon kicking off the project, Ergo Global carried out a full analysis of the facility and its staff. This included process analysis, employee surveys and employee observations.
9
900
Singapore
Laboratory
Surveys carried out revealed that no employee had received ergonomics training outside of a few forwarded ergonomics emails.
This had been a significant contributing factor in 65% of staff reporting discomfort within the last 12 months, with the majority coming from the most physically active departments of production and packaging.
This was the case in many processes between many operators, as shown by the table below…
Process
Awkward Postures
Short-term
Solution
Long-term
Solution
Weighing and dispensing heavy loads
Operators repeatedly twisted their bodies while weighing substances.
Move equipment around to line up better with the neutral body.
Use height-adjustable surfaces and implement an ergonomic break structure.
Dumping bulk bags
Operators often had to reach in front or overhead in order to load and dump heavy bags.
A simple but targeted stretching routine.
Centralisation of equipment and thorough ergo lifting training.
Packaging along an assembly line
Operators exhibited a lot of unnatural bending, twisting, reaching and lifting at various points along the assembly.
Reduce height of equipment and add platforms to minimise reach.
Reconfigure mechanisms and equipment to fit each individual worker.
Sample compositing
Operators spent much of their time in bent positions, twisting their torsos to move back and forth between samples.
Adjustable mobile chairs to reduce bending and twisting.
Replace laminar flow hood with a taller workstation for sufficient clearway.
In most roles within Abbott’s laboratory, there is some required use of a computer. The setup of each computer and the workstation around each computer was quite poor, leading to all sorts of issues, but predominantly neck, back and wrist discomfort.
These were the issues that our ergonomists found…
Diiscomfort
Problem
Short-term
Solution
Long-term
Solution
Shoulder discomfort
Many desks were either too high or too low. Operators were unable to work with their arms relaxed.
Use height-adjustable chairs to match the desk height.
Install keyboard trays under computer desks and use height-adjustable desks.
Back discomfort
Several chairs had no back support and were too high, leaving operators’ feet dangling and unable to support the back.
Use chairs with any kind of back support and use a stack of books to support the feet.
Use ergonomic chairs with adjustable back support and a footrest.
Neck discomfort
Operators were typically using monitors that were either too high or low, causing the neck to strain while looking at the screen.
Reposition monitors to be at eye-level by using books and other temporary makeshift solutions.
Use wall-mount brackets and adjustable monitors to be able to place monitors at perfect height and distance for each operator.
Although Abbott generally had a good environment in most sections of its facility, there were some sections with environmental ergonomic risks. These risks either weren’t addressed or were only partly addressed, which left operators at risk of an accident or a musculoskeletal injury.
Our ergonomists uncovered the following environmental issues…
Environmental
Risk
Reason for Risk
Short-term
Solution
Long-term
Solution
Wet floor
After dumping, operators cleaned the area using a hose. Water from this often spilled over into the operators’ walkway.
Fix the hose below the dumping platform so that water spray is limited to the cleaning area.
Same as short-term solution.
High noise level
Some areas, including the packaging hall and the dumping area, were high noise environments, creating risk for operators’ hearing.
Operators must wear ear plugs or overhead earmuffs at all times while working.
Build in a system of regular breaks in quieter areas. This will allow consistent respite from the noise.
Lack of clearance space
In the sample compositing part of the lab, operators often bumped their heads on low ceilings due to a lack of clearance space.
A height adjustable chair allows the operator to do their job while sitting.
Replace the laminar flow hood with a taller workstation to allow every operator sufficient clearway while standing.