Table of contents:
2. What is the industrial ergonomics checklist?
3. An ergonomics audit checklist for industrial workplaces
3.5 Handling aids and equipment
4. Why ergonomics assessment is important for the industry
5. Ergonomic guidelines for industrial work environments
6. The role of professional ergonomists in enhancing industrial workplace ergonomics
In 2021, workers at the US warehouses of a renowned online retailer experienced a greater frequency of injuries compared to their counterparts at other companies’ warehouses, according to a recent study.
The study found 5.9 severe injuries per 100 workers at this renowned online retailer, nearly 80% higher than the industry average. The studies’ organisers attribute the retailer’s “obsession with speed” as a primary cause of the problem. They failed to consider industrial ergonomics.
Don’t let your employees experience the same! Such occurrences can negatively impact your business reputation. It is time to consider undergoing an industrial ergonomics audit, although it is important to note that the auditing process should only be conducted by professional ergonomists.
Our Industrial Ergonomics Consulting can help you. Our Ergonomists are available to collaborate with you in order to reduce or eradicate ergonomic risks through the utilisation of well-established risk assessment approaches. The findings from these assessments enable our consultants to provide guidance on cost-efficient measures to mitigate any identified risks effectively.
There’s this tool called the industrial ergonomics checklist that professional ergonomists use for auditing. It helps prevent incidents, regardless if they are minor or severe, from happening at your employees’ workplace. Additionally, there are basic items on the industrial ergonomics auditing checklist that you can proactively address on your own to contribute to a safer and more ergonomic work environment.
Before you discover more about the industrial ergonomics audit checklist, you may want to read our blog about ergonomics assessment checklists in general.
This blog discusses what an industrial ergonomics checklist is, the risk factors it addresses, its importance, the industrial ergonomics standards, and more.
What is the industrial ergonomics checklist?
An industrial ergonomics checklist can serve as the framework to assess the ergonomic conditions within a workplace. It enables the identification of potential hazards that could contribute to employee discomfort, fatigue, or injuries.
The ergonomics checklist for an industrial workplace provides an overview of the essential factors for a safe and optimised work environment. The best part is that it can be tailored to fit the special requirements of different industries and job roles.
When you use the basic ergonomics checklist, you can take a closer look at different aspects of your industrial workplace to consider whether it meets ergonomics standards and keeps your employees safe and healthy. However, it is important to note that while using the basic ergonomics checklist can provide valuable insights, it is still advisable to engage the services of a professional ergonomist to ensure a thorough evaluation and implementation of proper ergonomic practices in the industrial workplace. Their expertise and knowledge can help identify specific needs and tailor ergonomic solutions that prioritise the safety and well-being of employees.
An ergonomics audit checklist for industrial workplaces
The factors encompassed in an ergonomic audit for industrial workplaces can be applied to your employees’ work environments. By integrating these factors into the setup of their industrial workplaces, you can improve the overall ergonomics and promote the well-being and efficiency of your workforce.
Here are the factors that an industrial ergonomics assessment can address:
The working environment
Lighting:
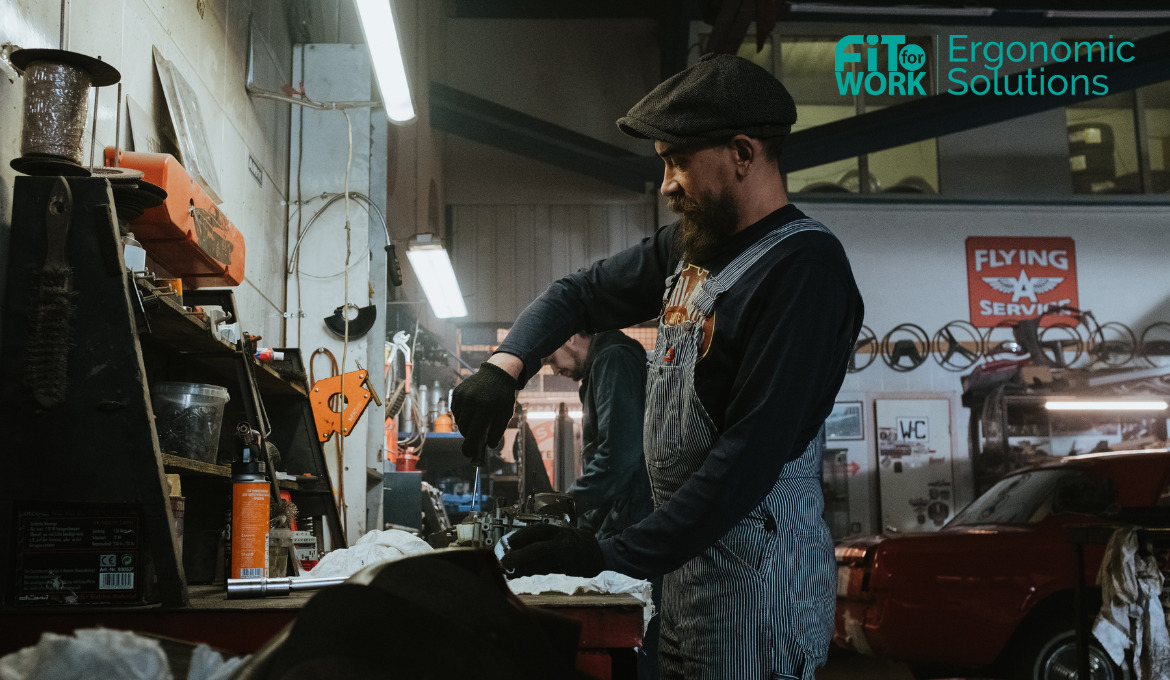
- Does the lighting level suit the tasks being carried out?
- Are there any glares or shadows that might lead to visual discomfort?
- Do any reflections or bright areas exist that could result in eye strain?
Noise:
- Are noise levels suitable for the specific work being conducted?
- Can any noise sources be removed or minimised?
Proper lighting is crucial for ensuring your employees can perform tasks efficiently and comfortably, as inadequate lighting levels, glares, or shadows can lead to visual discomfort and eye strain, potentially affecting productivity and well-being. Similarly, maintaining suitable noise levels in the workplace is essential for reducing distractions and stress, and minimising or eliminating noise sources can contribute to a more focused and pleasant work environment.
Are the tasks characterised by:
- Carrying loads away from the body?
- Engaging in twisting, stooping, or reaching upward movements?
- Involving significant vertical movements?
- Requiring long distances to carry items?
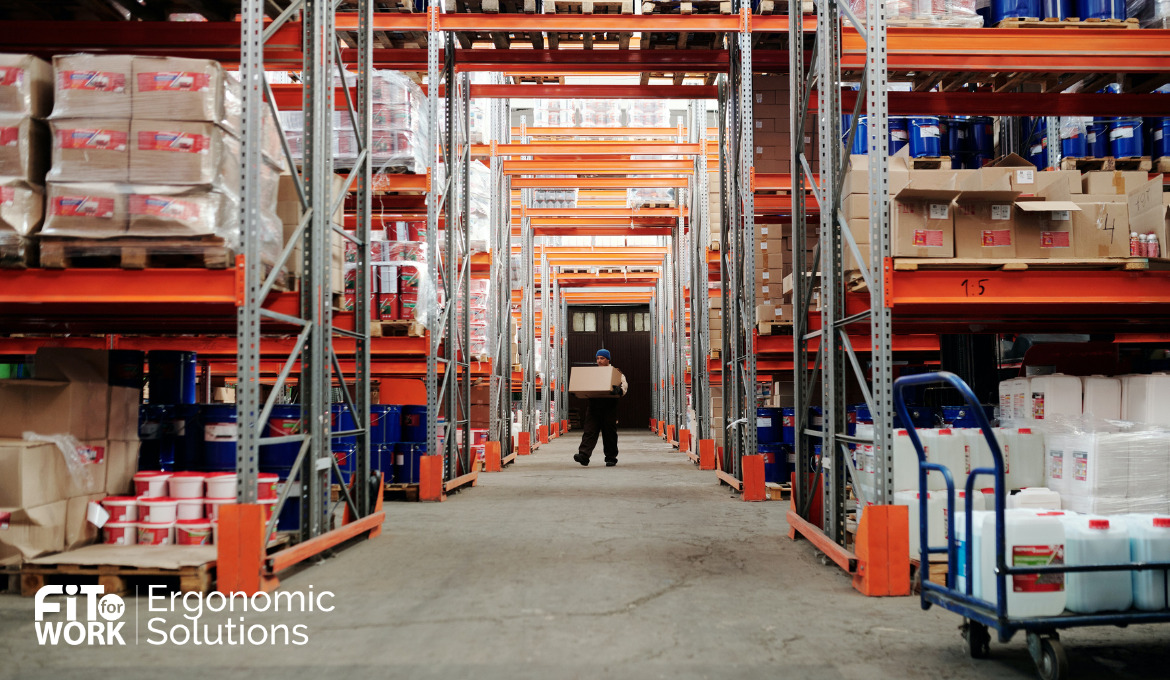
- Demanding strenuous pushing or pulling?
- Involving repetitive handling?
- Entailing a risk of sudden movement of loads?
- Insufficient rest or recovery time provided?
- Imposing a work rate dictated by a process?
Looking into the nature of tasks in the workplace is essential for identifying potential ergonomic problems and reducing the risk of injuries, such as back pain, among your employees. If your employees often experience back pain, explore our tips on how to prevent it.
Are the loads:
- Of substantial weight or size?
- Difficult to grip or hold?
- Nnstable or prone to unpredictable movement?
- Potentially harmful, such as being sharp or hot?
- Stacked in an awkward manner?
- Too large for the handler to have clear visibility over?
Assessing the properties of loads in the workplace is a vital component of an industrial ergonomics checklist, as it helps identify potential hazards and ensures employee safety. By addressing concerns related to the weight, size, stability (e.g., liquids in containers that may slosh or shift unexpectedly), and handling of loads, you can minimise the risk of accidents and injuries, ultimately fostering a more secure and efficient work environment for your staff.
Individual capacity
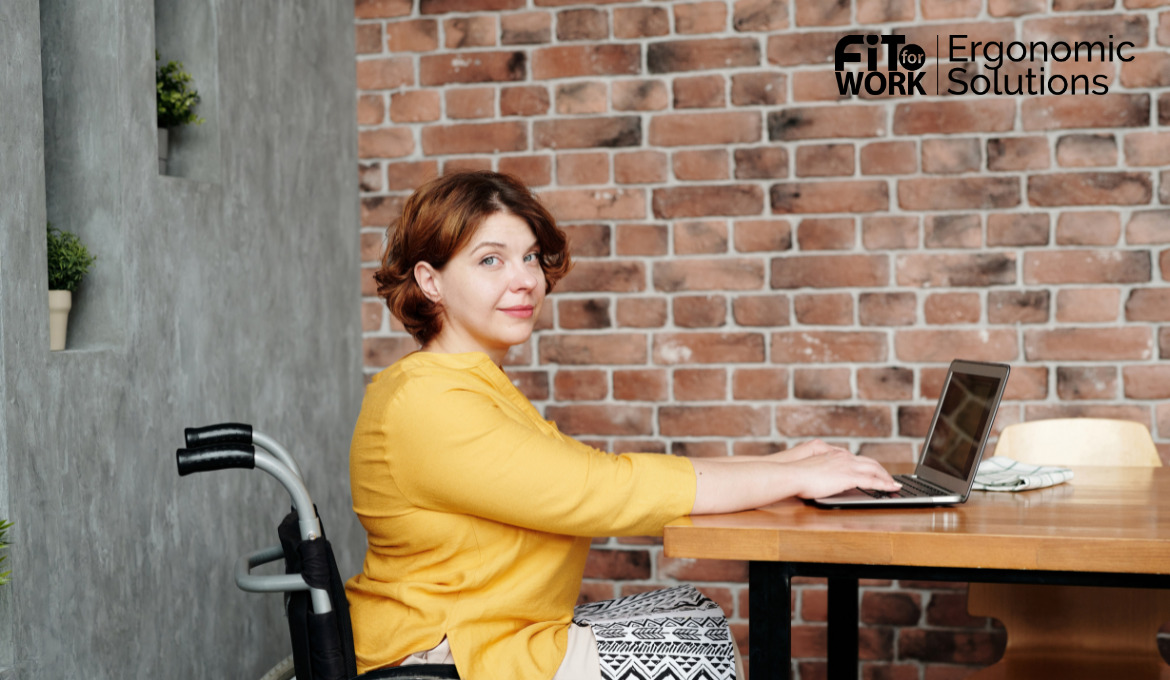
Does the job:
- Necessitate exceptional abilities, such as above-average strength or agility?
- Present a risk to individuals with health conditions or those with learning/physical disabilities?
- Pose a risk to new or expectant mothers?
- Pose a risk to inexperienced or young workers?
- Require specific information or training?
Addressing questions related to individual capabilities and risks in an industrial ergonomics checklist helps employers identify potential challenges and adapt their work environment accordingly. For instance, tasks that require exceptional abilities, such as lifting heavy objects or navigating tight spaces, can be evaluated and modified to better accommodate diverse employee needs, ultimately supporting a more accessible and efficient workplace.
Handling aids and equipment
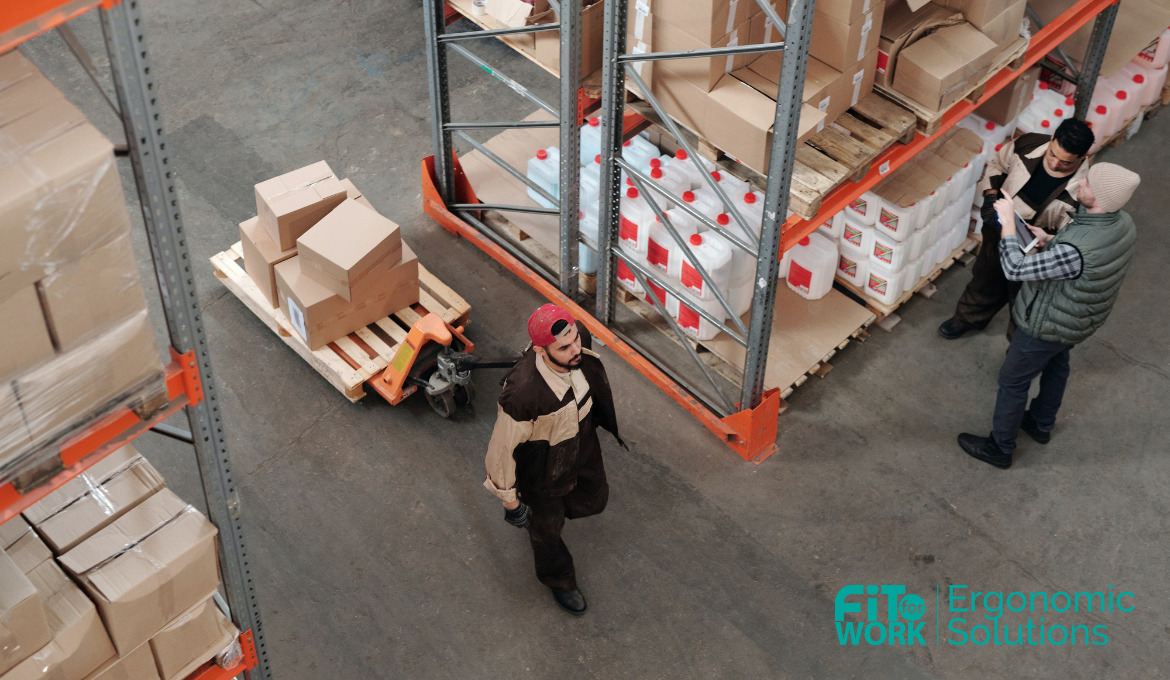
- Is the equipment appropriate for the task at hand?
- Is the device properly maintained?
- Do the wheels match the floor surface type?
- Are the wheels functioning smoothly?
- Is the handle positioned between waist and shoulder height?
- Are the handle grips in good shape and comfortable to hold?
- If brakes are present, are they functioning correctly?
Including these considerations about handling aids and equipment in an industrial ergonomics checklist is truly valuable. By focusing on the suitability, maintenance, and functionality of these devices, you will be able to enhance workplace safety and contribute to a smoother workflow, making your employees’ daily tasks more manageable and enjoyable.
Work organisation factors
- Is the nature of the work repetitive?
- Is the work pace dictated by machines or systems?
- Do employees perceive the workload as overly demanding?
- Do workers have limited control over their tasks and methods?
- Is there a lack of effective communication between management and employees?
These questions will allow you to understand where the risks are, but you need to engage our services to then put the plans in place to mitigate the risks. Our expertise will ensure comprehensive measures are put in place to minimise the identified risks and promote a safe and healthy workplace.
Ergonomics does not only work on tangible risk factors; it also considers employee mental well-being. Read more about it on our blog about employee wellness programs.
The good news is we don’t only offer ergonomics services! If you think your workers need a break, chat with us and ask about our Wellness Event Organisation.
Why ergonomics assessment is important for the industry
Every year in the US, accidents and health issues at work cost the nation a huge amount of money. According to the 2021 Workplace Safety Index by Liberty Mutual, companies spent over $1 billion each week on workers’ compensation for serious but non-fatal workplace injuries in 2018. The National Safety Council found that in 2019, job-related deaths and injuries had a combined cost of $171 billion for the country, businesses, and individuals.
Given these staggering costs associated with workplace accidents and health issues, it is crucial for employers to prioritise ergonomics and well-being in their work environments. One primary way to achieve this is by utilising the basic ergonomic assessment checklist for manufacturing to understand risks and then engage professional services.
Ergonomic guidelines for industrial work environments
In industrial work environments, ensuring the well-being and safety of workers is of utmost importance. Industrial ergonomics plays a vital role in promoting efficiency, productivity, and reducing the risk of work-related injuries. The following are the general ergonomic tips for manufacturing:
- Maintain proper posture.
- Adjust workstations.
- Provide adequate lighting.
- Reduce excessive noise.
- Use proper lifting techniques.
- Avoid repetitive motions.
- Optimise work height.
- Encourage regular breaks.
- Provide personal protective equipment (PPE).
- Provide training and education.
- Undergo regular ergonomic assessments.
Remember that evaluating the ergonomic safety of your manufacturing operations industrial ergonomics involves assessing and analysing the ergonomic aspects of your manufacturing processes to ensure a safe working environment. While an audit typically involves an evaluation that focuses on the overall assessment and analysis of ergonomic safety.
By involving your employees in an audit using the basic industrial ergonomics checklist, you can gain firsthand knowledge about their experiences and gather valuable input for potential enhancements through ergonomics.
The role of professional ergonomists in enhancing industrial workplace ergonomics
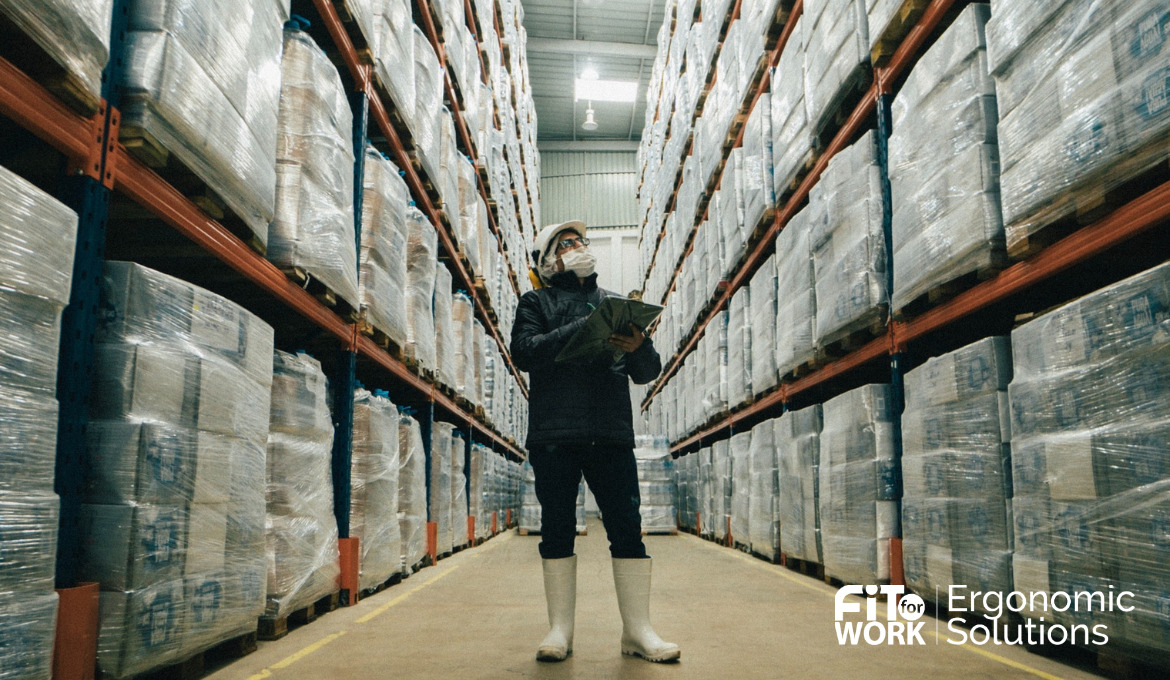
In the realm of industrial workplaces, the implementation of a basic industrial ergonomics checklist template is helpful. However, to further elevate the results, the involvement of professional ergonomists like us in Fit For Work becomes crucial. With our assistance, you can maximise the effectiveness of the checklist and enhance the overall ergonomics of your industrial workplace.
Here are some ways we contribute to the checklist’s effectiveness:
- Expertise and Knowledge: We can bring extensive knowledge and expertise in ergonomics. We identify relevant factors and criteria to include in the checklist. We also ensure that the checklist comprehensively covers all important aspects of ergonomic evaluation.
- Customisation: We tailor the checklist to suit the specific needs and requirements of the industrial workplace and consider the unique characteristics, tasks, and potential risks associated with the environment. We want the checklist to be relevant and applicable.
- Accuracy and Validity: We make sure that the checklist items are based on evidence-based practices and scientific research and validate the checklist to ensure its accuracy and reliability in identifying ergonomic hazards and risks.
- Integration of Regulations and Standards: We incorporate relevant regulations, standards, and guidelines into the checklist, aligning it with industry best practices and legal requirements. This ensures compliance and helps organisations maintain a safe and healthy workplace.
- Risk Assessment: We use the industrial ergonomics checklist as a tool for conducting comprehensive risk assessments. We analyse the collected data to identify potential ergonomic hazards and prioritise them based on their severity and likelihood. This enables you to focus your efforts on addressing the most critical risks.
- Recommendations and Controls: We provide practical recommendations and cost-effective controls to address the identified risks. We also suggest ergonomic interventions, modifications, and improvements that can mitigate hazards, reduce the risk of injuries, and enhance overall ergonomic conditions in the workplace.
- Training and Education: We offer training sessions and educational programs to help you understand and implement the checklist effectively. Just visit our Ergonomic Trainings page and learn how we can provide comprehensive education on ergonomics.
Ensuring workplace well-being through the industrial ergonomics checklist and professional intervention
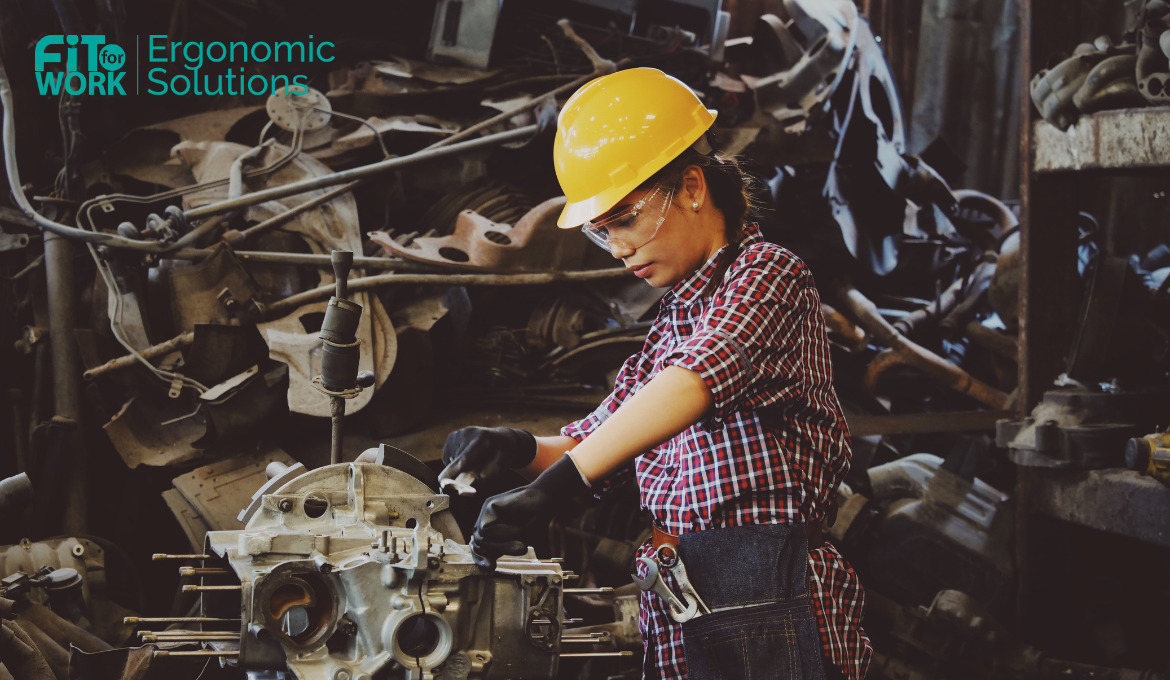
Incorporating an industrial ergonomics assessment checklist, along with the assistance of professional ergonomists, can significantly contribute to the success of your business. By proactively addressing potential hazards and optimising the work environment, you can minimise workplace injuries and illnesses, which in turn reduces workers’ compensation costs and boosts employee well-being.
Now is the time to take action by availing of our Industrial Ergonomics Consulting service. Our team of ergonomics professionals will work closely with you to identify potential hazards, provide tailored solutions, and make a safer, more efficient workplace for your employees.